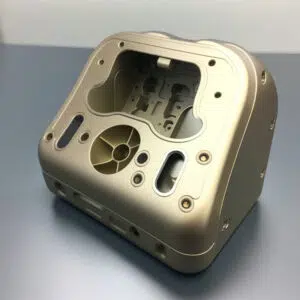
CNC machining has revolutionized the manufacturing industry by enabling the creation of precise, intricate parts from a variety of materials. Utilizing computer-aided design (CAD) software to generate toolpaths, CNC machines precisely control cutting tools to remove material and shape workpieces with exceptional accuracy. This technology is particularly well-suited for complex designs that would be challenging or impossible to achieve using traditional methods.
From aerospace components to medical implants, the applications of CNC machining are vast and diverse. Its versatility allows manufacturers to produce parts of varying sizes, shapes, and tolerances with exceptional repeatability. The ability to automate the manufacturing process through CNC programming also improves efficiency and reduces lead times, making it a highly desirable choice for modern production.
Unlocking Accuracy and Efficiency with CNC Machining
CNC machining has revolutionized the manufacturing industry by providing precise control over material removal. CNC machining This automated process utilizes computer-aided design (CAD) software to generate toolpaths that guide a robotic milling machine, lathe, or other fabrication equipment. The result is exceptional parts with tight tolerances and repeatable accuracy, exceeding the capabilities of manual machining methods.
One of the key benefits of CNC machining is its ability to enhance efficiency. By automating repetitive tasks and allowing for continuous operation, CNC machines can significantly reduce lead times and increase production output. Furthermore, CNC programming enables intricate designs and complex geometries that would be challenging or impossible to achieve through traditional methods.
The versatility of CNC machining extends across a wide range of industries, from aerospace and automotive to medical device manufacturing. Its adaptability to various materials, including metals, plastics, wood, and composites, makes it an invaluable tool for diverse applications.
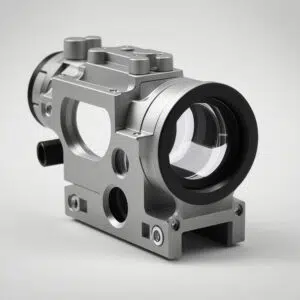
Delving into the World of CNC Milling and Turning
The realm of CNC machining presents a captivating landscape for both seasoned professionals and enthusiastic novices. CNC milling and turning, two cornerstones of this field, empower manufacturers to craft intricate components with exceptional precision and efficiency. Milling leverages rotating cutters to remove material from a workpiece, shaping it into complex geometries. Conversely, turning involves rotating the workpiece against a stationary cutting tool, creating cylindrical or conical shapes. From prototyping delicate devices to mass-producing robust engine parts, CNC milling and turning have revolutionized various industries.
- Mastering the intricacies of CNC programming opens doors to a world of limitless design possibilities.
- Applications such as CAM (Computer-Aided Manufacturing) translate intricate designs into precise machining instructions.
Additionally, advancements in tool materials and cutting techniques persistently push the boundaries of what's achievable with CNC milling and turning.
Move From CAD to CAM: The Power of CNC Programming
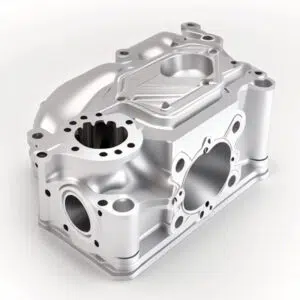
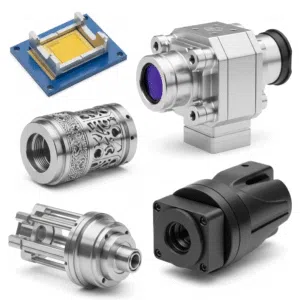
The world of manufacturing has been revolutionized by the seamless integration of Computer-Aided Design (CAD) and Computer-Aided Manufacturing (CAM). This dynamic duo empowers engineers and machinists alike, streamlining the process from design conception to physical production. At the heart of this transformation lies CNC programming, a specialized language that guides computer-controlled machines to execute intricate tasks with remarkable precision. CNC programmers act as the bridge between CAD models and the real world, translating complex geometrical designs into a series of precise instructions that dictate the movement of cutting tools. This complex code brings digital blueprints to life, enabling manufacturers to produce parts with unmatched accuracy, repeatability, and efficiency.
The benefits of CNC programming are far-reaching. It improves productivity by automating complex operations, reducing manual labor and minimizing human error. Moreover, it opens doors to the creation of highly intricate and customized designs that were previously unattainable through traditional methods. From aerospace components to medical implants, CNC machining has become an indispensable tool in a wide range of industries. The future of manufacturing lies on this powerful synergy between CAD, CAM, and CNC programming, continuously pushing the boundaries of what's possible.
Cutting-Edge Materials in CNC Machining: Redefining Limits
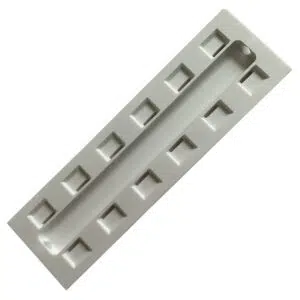
The realm of CNC machining continuously evolves as advancements in materials science unlock unprecedented possibilities. Engineers and manufacturers|Fabricators and designers are now harnessing a diverse array of advanced materials, pushing the boundaries of what's achievable through CNC fabrication. From lightweight composites to high-strength alloys, these innovative materials present unique challenges for machinists and designers alike.
- High-performance polymers|Lightweight metals|Ceramic-matrix composites
- Enhanced strength|Improved wear resistance
- Intricate detailing
This dynamic shift in materials demands a deep understanding of their properties and machinability.
CNC machine operators|Skilled machinists must leverage advanced knowledge to optimize cutting parameters.
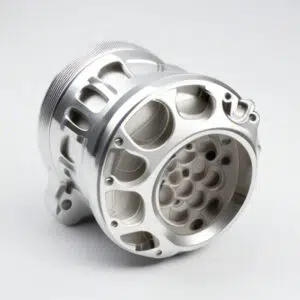
The Future of Manufacturing: Embracing CNC Technology
As the manufacturing landscape continues to evolve at a rapid pace, embracing cutting-edge technologies is paramount for success. One such transformative technology that is reshaping the industry is Computer Numerical Control (CNC) machining. This sophisticated systems empower manufacturers to achieve unparalleled precision, efficiency, and customization in their production processes.
CNC technology enables manufacturers to create complex geometries with exceptional accuracy, reducing reliance on manual labor and minimizing human error. Furthermore, CNC machines can operate continuously, maximizing productivity and output. The versatility of CNC machining facilitates the production of a wide range of parts from various materials, fulfilling the diverse needs of modern manufacturing.
- CNC technology is rapidly becoming an essential component of Industry 4.0, enabling the seamless integration of manufacturing processes with digital automation and data analytics.
- The adoption of CNC machines results to significant cost savings by reducing material waste, optimizing production cycles, and minimizing labor requirements.
- With its ability to produce intricate designs and high-precision components, CNC machining is driving innovation in various sectors, including aerospace, automotive, and medical devices.
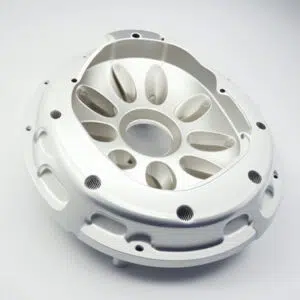
As the demand for personalized products grows, CNC technology will play an even more pivotal role in enabling on-demand manufacturing and rapid prototyping. Embracing CNC machining is not simply a technological advancement but a strategic imperative for manufacturers who seek to remain competitive in the ever-evolving global market.
Streamlining CNC Processes for Reduced Lead Times
In today's competitive manufacturing landscape, reducing lead times is paramount to success. CNC machining offers exceptional precision and efficiency, but there are always opportunities to fine-tune processes further. By integrating best practices, manufacturers can substantially reduce lead times and boost overall productivity. This involves a multi-faceted approach that includes analyzing workflow bottlenecks, exploiting advanced software tools, and allocating in state-of-the-art CNC equipment.
Troubleshooting Common CNC Machining Issues
CNC machining is a precise and efficient process, but like any manufacturing technique, it can encounter problems. Identifying and resolving these issues promptly is crucial for maintaining productivity and ensuring high-quality final products. One common problem involves tool wear. Over time, cutting tools become dull and lose their effectiveness, leading to rougher surfaces and increased machining times. Regularly inspecting and replacing worn tools can significantly improve machining accuracy.
Another frequent challenge is improper feed rates and speeds. Setting these values incorrectly can result in excessive tool wear, poor surface finishes, or even machine failure. Carefully calibrating the feed rate and speed based on the material being machined and the tool used is essential for optimal performance.
CNC machines are also susceptible to vibrations during operation, which can cause inaccuracies and damage to parts. Ensuring proper tooling selection, balancing rotating components, and implementing vibration damping techniques can mitigate these issues. Regular maintenance, including lubrication and cleaning, is critical for preventing wear and tear on machine components, ensuring smooth operation, and extending the lifespan of your CNC equipment. By addressing these common machining problems, you can maintain high production standards and achieve desired outcomes.
Computer Numerical Control machining for Rapid Prototyping and Low-Volume Production
CNC machining offers a flexible solution for both rapid prototyping and low-volume production runs. Its ability to create complex geometries with high accuracy and repeatability makes it ideal for bringing designs to life quickly. Whether you're developing a prototype to test functionality or producing a limited number of custom parts, CNC machining can deliver precise results within a reasonable timeframe. The process involves using computer-controlled tools to remove material from a workpiece, guided by digital blueprints. This allows for intricate detailing and the creation of parts with tight tolerances, making it suitable for a wide range of industries, including aerospace, automotive, and medical device manufacturing.
- Pros of CNC machining include:
- High detail
- Rapid Production
- Budget-Friendly for low-volume runs
- Ability to create complex geometries
The Value Proposition of CNC Machinery
Businesses seeking to boost efficiency and production capacity often consider investing in Computer Numerical Control (CNC) machinery. These advanced machines offer a wide range of benefits, providing increased precision, reduced lead times, and enhanced product quality.
The return on investment (ROI) for CNC machinery can be substantial, fueled by factors such as lower labor costs, minimal material waste, and the ability to produce complex designs with ease.
- CNC machines can significantly decrease production times compared to traditional methods, enabling businesses to meet tight deadlines and accommodate customer demands effectively.
- The high precision of CNC machining results in products with consistent quality and dimensional accuracy, surpassing industry standards and customer expectations.
- By automating repetitive tasks, CNC machinery frees up human resources for more complex operations, enhancing overall productivity.
Moreover, the versatility of CNC machines allows businesses to produce a wide variety of products from different materials, expanding their production capabilities and market reach.
Master CNC Code: A Comprehensive Guide
Embark on a journey to dominate the world of CNC programming with our all-inclusive guide. From fundamental concepts to advanced methods, we'll equip you with the knowledge and skills to design intricate parts with precision. Learn about G-code syntax, toolpaths, feed rates, and more as we explain the intricacies of CNC code. Whether you're a beginner or a seasoned craftsperson, this guide will boost your CNC programming capabilities to new heights.
- Explore the fundamental elements of G-code and M-code.
- Master various toolpaths for diverse machining operations.
- Optimize feed rates and speeds for optimal results.
- Visualize your CNC program before execution.